RUBBER MOLDED PARTS MANUFACTURER / RUBBER-METAL MOLDED PARTS
Quality from our EU production is important to us
As a manufacturer of molded rubber parts, we are a partner to industry throughout Europe for application technology solutions. We supply customers in the process industry (chemicals, pharmaceuticals, petrochemicals), the automotive and electrical industries, mechanical engineering and agriculture.
With international experience, strong solutions and flexibility, we supply both customized solutions and numerous standards.
As a manufacturer of rubber molded parts and rubber-metal molded parts, we work together with renowned compound manufacturers from the EU. Regardless of whether resistance to aggressive chemical media is required, approval in accordance with a food approval or drinking water regulations, we try to find a high-quality solution with our compounders. The production processes for the molded parts are determined depending on the quantity and geometry. Regardless of the batch size, whether small, medium or large series, we select the economically and technically best alternative. In doing so, we also take into account the tolerances required by our customers and what is possible in terms of production technology.
We supply molded rubber parts made of NR, CR, NBR, HNBR, EPDM, VMQ (silicone), fluorosilicone, FPM / FKM, etc.
Wherever oscillations and vibrations need to be damped or absorbed, we offer rubber-metal connections according to the requirements. We produce special rubber-metal parts according to drawings and also offer standard rubber vibration dampers, rubber buffers, bushings and ring elements, machine feet, conical bearings, adjustable feet and bumpers. The materials used for these rubber-metal compounds are mostly natural rubber NR, CR chloroprene rubber or EPDM.
When designing the composite bodies, the conditions of use and the resulting stresses on the elastomers must be taken into account. It should be noted that elastomers can withstand stresses caused by shear and compression in the long term, whereas tensile stresses can lead to premature failure due to ozone or fatigue cracks and must therefore be avoided.
The dynamic properties are frequency-, amplitude- and temperature-dependent and the elastomer should be selected accordingly.
Standard manufacturing tolerances are according to DIN ISO 3302-1 class M2 or M3
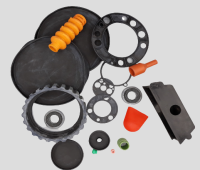
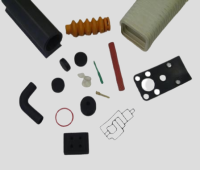
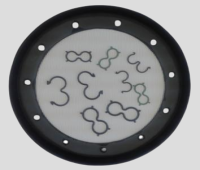
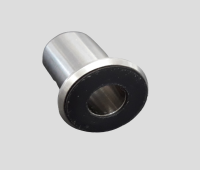